VOCON
The most advanced inline configurable VOCON system on the market today. VOCON complies with the latest rules and regulations and is equipped with the most advanced reporting system anywhere. Designed for the oil carrier market, our VOCON system gives greater protection to your cargo and crew.
Protect your cargo, crew and the environment -while reporting on emissions
The VOCON system is developed by Intertanko outlining how to limit the manual release to a tank pressure around the TVP of the cargo, rather than far below it. It is a prudent and logical step forward in managing cargo loss and involves two pieces of equipment:
a) Constant pressure valves.
b) An automated release valve that operates according to the VOCON procedure.
The individual valves are referred to as the VOC stop system. The central, automated system for gas release is referred to as the VOCON valve system.
The key element of the VOCON valve system is a centralised release valve that features:
- Remote-controlled opening and closing.
- Automatic reflection of cargo temperature changes.
- The system is primarily used on oil carriers.
The system works with electrical actuators, or with a self-contained Ex-approved electric actuator. The opening and closing pressure are remotely controlled from the C.C.R. via a PLC-unit.
Highly suitable for the oil carrier market
The VOCON system is developed in accordance with the guidance IMO/MSC/Circ. 680 requirement of controlling the VOC emissions from cargo tanks on a COT.
The VOCON system is developed in accordance with IMO Resolution MEPC.185(59) guidelines for the development of a VOC management plan to ensure that the operational procedure is optimised to minimise VOC emissions.
The VOCON system is designed and sized under API 2000 requirements for breathing purposes to minimise the emission of VOC for COT/VLCC size vessels.
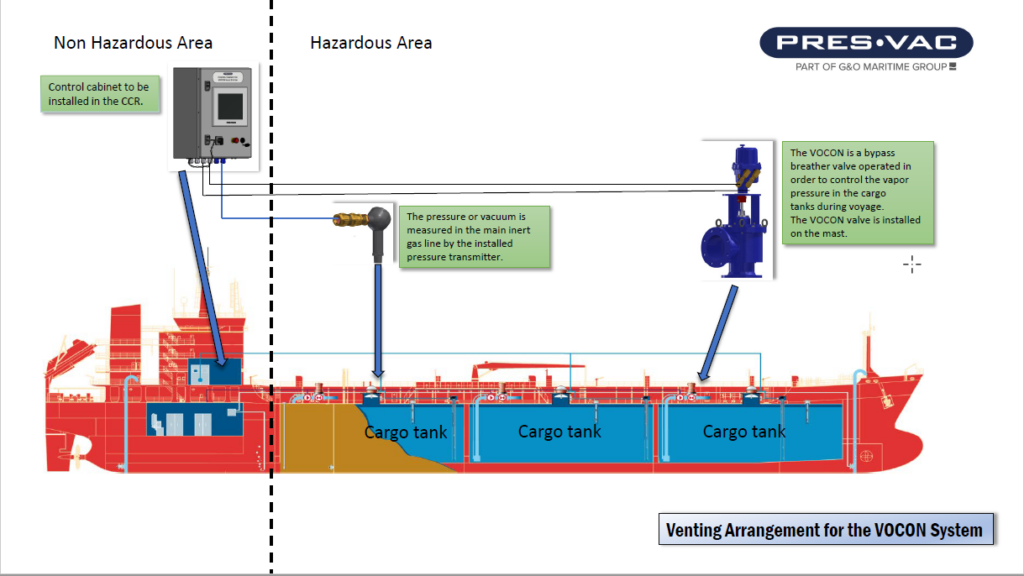
Design
VOCON an automated system capable of maintaining a constant pressure span during the voyage.
The VOCON venting system is controlled by an electrical actuator maintaining the tank pressure between the set-pressure and the re-seating pressure. The system is installed on the mast riser bypass line and controls the vapour pressure in all the cargo tanks during the voyage for direct emission control. By controlling the pressure in the venting system, it is possible to fully control the VOC emissions.
The system can be programmed to enable adjustment of the opening setting on the valve, according to what is optimal for the specific cargo.
Design features
Electrical actuator
The valve actuator is analogue controlled and can be set to open partly instead of full. This feature can be used to reduce the flow rate for measuring more accurately and keep the pressure on the cargo avoiding boil off. Approved for hazardous area installation.
VOCON valve
A built-up piston controlled inline pressure vacuum valve in stainless steel for breathing purposes and full flow capacity performance. Covering a range from 2.400 Nm3/h to 26.000 Nm3/h.
Control cabinet
The system is operated from an HMI (Human Machine Interface) touch screen in the front of the cabinet. It is possible to run in automatic or manual. Settings can be adjusted within the max/min limitation for safe operation. The control cabinet must be placed indoors in a non-hazardous area, e.g. in the Cargo Control Room.
Pressure transmitter
The relative pressure transmitter (gauge pressure) is placed on the IG Main line. The transmitter is used to measure the pressure in the tank venting system and reports back to the control cabinet for action. Approved for hazardous area installation.
Contact us
By filling out this form, your request will be shared directly with our experts. We will reply as soon as possible.